塑料注塑工艺:是指把塑胶原料熔融后通过注射端注入模具中,冷却成型后达到预定形态的一种塑料成型技术。注塑设备包括入料端、熔融端、注射端、模具及合模装置等主要部件,通过各部件之间不同的组合控制,可以对不同属性的材料进行相应的注塑成型。
注塑成型工艺流程一般包括六个阶段:熔料–合模–填充–保压–冷却–脱模
一、熔料阶段
不同材料有不同的熔融温度,低于该温度则熔料不透,超过该温度则会焦化出现黑点等问题,所以熔料阶段的温度控制相当重要;根据不同材料选择不同熔融温度,另外小范围的温度变化还可以作为产品不良现象的处理手段;
二、合模装置
合模是指把模具A、B面紧密贴合在一起的步骤,合模的原则是保持模具贴合的稳定性,在注射压力的冲击下仍保持紧密的贴合度,不产生缝隙和位移现象;越是精密的产品对合模要求越高,越是精密的合模技术越能注出高品质的产品,合模技术也是注塑技术不断进步的指标之一;
三、填充阶段
填充是注塑循环的第一步,当喷嘴把熔融状态的原料注入模具时,原料随着模具的空隙游走,填充满各个空间,一般填充率达到95%之后开始进入保压阶段;理论上填充时间越短,成型效率越高,但在实际成型过程还受到很多条件制约,比如模具结构、流道、浇口、冷料井等等;
四、保压阶段
保压是在填充完毕的情况下,对注射通道施加持续压力的过程,这个过程是为了压实熔体、增加塑料密度以及补偿塑料的收缩行为;保压过程中注塑螺杆仍缓慢移动,塑料在模壁冷却固化过程加快,熔体粘度上升,模内阻力不断上扬,材料密度持续增大,塑件完成成型,此时保压压力达到顶峰;保压过程中的合模锁力要求最为严格,稍有松动就会产生不良产品,因此合模装置性能高低表现在这里了;
五、冷却阶段
熔料在进入模具后由于温差开始固化,在固化过程中会产生许多变化,熔料只有固化到一定刚性才能顺利脱模成为合格的产品,冷却固化的周期约为整个成型周期的70%-80%,因此,缩短冷却时间是提升注塑效率的主要方法;影响冷却时间的主要因素有,模具设计、模具材料、冷却水管配置方式、冷却液流量、冷却液性质、注塑材料等,合理控制这些方面对提升注塑效率影响甚大;
六、脱模阶段
脱模是注塑成型最后一个阶段,原则就是脱模力的均匀施放,均匀脱模可以避免产品由于受力不均而产生的变型、损坏及出现顶痕等缺陷;常用脱模方式主要有顶杆脱模和脱料板脱模两种,合理运用脱模方式是提升注塑合格率的重要手段,特别是在注塑透明制品时,脱模方式的优化达到最大要求;
注塑工艺的技术参数
一、注塑压力
在整个熔料填充过程中所需的注射压力就是注塑压力,是由注塑设备的液压系统提供;注塑压力克服了熔体流动过程中的阻力,使熔料经由喷嘴进入模具的竖流道、主流道、分流道,经浇口进入模具型腔。
影响注塑压力的几个因素有:材料流动性能、模具结构及产品厚度、模具排气系统、成型工艺要素等;
二、注塑时间
注塑时间是从填充开始到保压开始之间的这段时间,一般注塑时间都很短,约占整个注塑过程的10%-15%,虽然注塑时间对成型周期影响不大,但是对于浇口、流道和型腔的压力控制影响很大,合理的填充时间有利于提高产品表面质量度及降低产品尺寸公差程度;利用注塑时间可以反推出冷却时间范围,可以作为优化注塑效率的一个辅助系数;
三、注塑温度
注塑温度是影响注塑压力的主要因素。原料从料桶进入料筒之后会经过5-6个加热段,每个段位的温度都不同,根据不同材料的熔融温度范围,适当控制温度是注塑成败的关键;如果温度过低,熔料塑化不良,会影响成型质量,增加工艺难度,如果温度过高,则会引起焦化分解,造成黑点及气泡等不良现象;现实注塑过程中,注塑温度往往比料筒温度要高出许多,根据材料的不同,最高温差可以达到30℃左右,在作模流分析时,温差问题也必需考虑入内;
四、保压压力和保压时间
在注塑过程将近结束时,螺杆停止旋转,只是向前推进,此时注塑进入保压阶段。保压过程中注塑机的喷嘴不断向型腔补料,以填充由于制件收缩而空出的容积。如果型腔充满后不进行保压,制件大约会收缩25%左右,特别是筋处由于收缩过大而形成收缩痕迹。保压压力一般为充填最大压力的85%左右,保压时间需根据产品的体积及冷却成型时间长短来决定,一般为注口处熔料固化时间为佳,正确的保压压力和保压时间是控制产品不良率的重要手段;
五、背压
背压是指螺杆反转后退储料时所需要克服的压力。采用高背压有利于色料的分散和塑料的融化,但却同时延长了螺杆回缩时间,降低了塑料纤维的长度,增加了注塑机的压力,因此背压应该低一些,一般不超过注塑压力的20%。注塑泡沫塑料时,背压应该比气体形成的压力高,否则螺杆会被推出料筒。
注塑加工优化措施
注塑成型工艺并不是一成不变、顺理成章的,由于产品的不同、材料的不同、注塑机器的不同以及材料预处理等等条件的不同,注塑过程会产生许多不确定的因素,所以作为注塑加工工作者,针对具体情况对加工过程进行相应的优化调整是体现注塑加工技术的最高体现。
注塑加工优化具体可以从以下几方面开展:
1、材料的预处理
根据不同材料的吸水性不同,有些材料在加工前需要先烘干,去除材料中的水分,以降低注塑过程中不良品的比例;
2、注塑设备状态保持
注塑机是高精密设备,其中各种系统的分工合作默契度要求很高,保持良好的工作状态不但可以更高效的运作,而且可以降低产品生产过程中的不良机率;
注塑机保养包括:防尘处理、润滑处理、损耗配件的更新、紧固螺丝的复位、压力系统的校准等等;
3、模具设计优化
模具在开发过程中需要根据应用原料的基本属性进行开发,不同的收缩率、不同的吸水性和不同的成型流动性能都需要考虑在内,设计好模具腔体内熔体的流动走向、压力均匀和气体排放等条件,是降低注塑难度,提升生产效率的重点组成,高效的成型模具非常重要;
4、模具的保养
高效的模具固然重要,但是保持模具一贯的高效运作也是非常重要的,保持模具良好主要有:保持模具的清洁、避免磨损、损耗件的及时更换、保持润滑、控制好温差影响、及时调整状态等等;
如何有效的提升注塑加工的效率,除了以上注塑设备的良好运作、模具的良好表现和材料属性的充分了解之外,还需要操作人员在长期生产中不断的研究和尝试,才能更高效更高质的加工出良好的产品。环科精密多年的塑料服务经验,成就了高效高质的注塑加工服务,为广大客户带来不一样的产品体验。
扩展:注塑机的分类
1、按照原料塑化和注射方式分: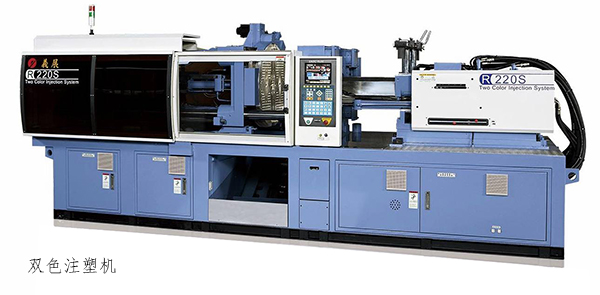
A、柱塞式注塑机;
B、往复螺杆式注塑机;
C、螺杆塑化柱塞注射式注塑机;
2、按外观结构分:
A、立式注塑机;
B、卧式注射机;
C、角式注射机;
D、多模注射机;
E、组合式注射机;
3、按加工能力大小分:
A、超小型注射机;
B、小型注塑机;
C、中型注塑机;
D、大型注射机;
E、超大型注塑机;
4、按应用用途分:
A、通用型注射机;
B、排气式注射机;
C、精密度高速注射机;
D、塑料鞋用注射机;
E、三注射头单模位注射机;
F、双注射头两模位注射机;